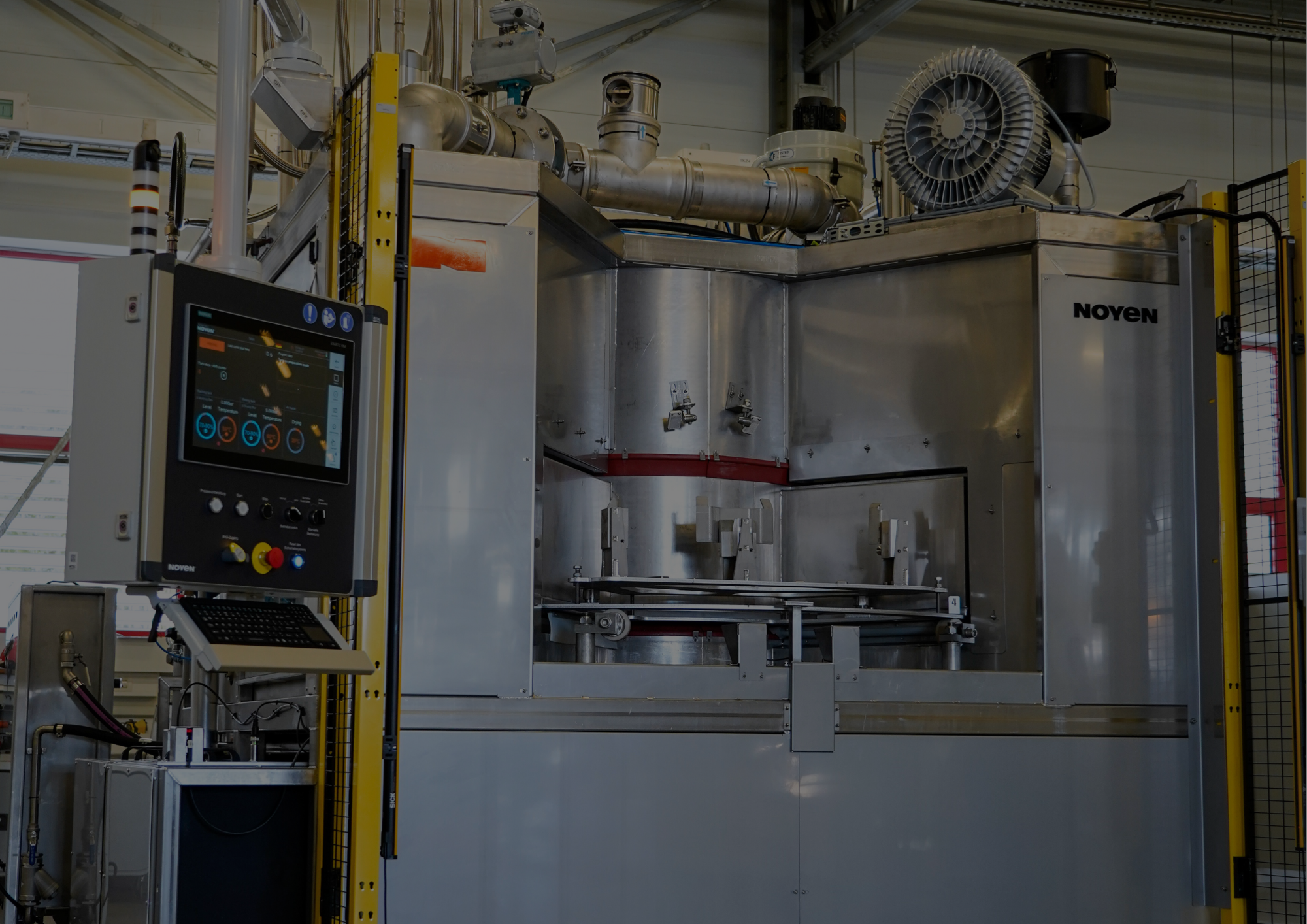
Automated Cleaning of Brake System Components for Heavy-Duty Vehicles
Our long- term client specializes in the production and machining of castings for OEM manufacturers in the automotive industry. One of the challenges that arose as a result of the CNC machining and pressing of complex brake calipers was the need to clean these components in accordance with technical cleanliness standards.
What did the client need?
After the CNC machining and pressing process, the calipers were covered with coolant. In addition to oily contaminants, numerous chips were present, including in through-holes and threads. The client tasked us with developing a solution that would meet both quality and performance requirements while being integrable with their existing robotic production line.
The cleanliness standards set for the project included:
- Maximum 250 µm for metallic particles,
- Maximum 400 µm for non-metallic particles (excluding fibers).
The solution:
To meet the client’s requirements, we proposed a NOYEN Expert C cleaning machine with dimensions of 2850 x 4400 x 2850 mm. The machine was designed for both manual and automated operation, with the possibility of loading and unloading using a robot. The client handles nearly 40 different part references, which required the development and implementation of retoolable tooling.
Cleaning process stages:
- Spray washing
- Spray rinsing
- Hot air drying
- Vacuum drying
The cleaning cycle time was 50 seconds per part, and the loading area could accommodate two parts at a time. A key element was the precise configuration of the spray nozzles, which effectively cleaned complex areas such as blind holes and threads where contaminants such as metal chips accumulated.
Due to the short cycle time, the drying process was divided into two sections: hot air drying and vacuum drying. This division increased the efficiency of drying – hot air heated the parts, and the vacuum completed the process by evaporating water under low pressure conditions. The use of a dedicated vacuum chamber, which has proven itself in many applications, allowed for even better drying results.
To increase the bath’s durability NOYEN’s team of technologists implemented a filtration system and oil separator, which extended the bath life to up to six weeks.
Operator safety was ensured by installing a light curtain, which prevented machine operation when an operator was in the robot’s working zone. The HMI panel allowed full control over the process and the creation of dedicated programs. Additionally, the machine was integrated with the client’s electronic database, enabling data exchange between machines on the production floor.
Customer benefits:
- Compliance with high-quality standards (max. 250 µm for metallic particles and max. 400 µm for non-metallic particles), ensuring the highest cleanliness of components.
- Operator safety through the use of modern safety systems like the light curtain.
- Bath lifespan extended to up to 6 weeks thanks to the implemented filtration system and oil separator.
- Compact machine design saving floor space in the production hall.
- Flexible operation – the machine could operate in both manual and automatic modes, increasing flexibility and production efficiency.
What does our clinet say about the project?
The client chose to work with us based on recommendations from other companies where we had successfully implemented automated cleaning lines. The key advantages they identified during the project included:
- Automated loading and unloading, which optimized processes and allowed human resources to be redirected to other production areas.
- Versatility of the cleaning machine, which was prepared to clean a wide variety of part references.
- Energy efficiency, achieved through solutions such as tank insulation and heat recovery from vapors, which helped reduce operational costs.
- Increased bath life due to the filtration system and oil separator.
Summary:
Through the implementation of advanced washing technology, our collaboration with the client contributed to improved production quality, increased efficiency, and enhanced process safety. The NOYEN Expert C machine proved to be a key element in achieving the client’s production goals, and the solutions applied in the project delivered lasting benefits in both performance and cost savings.
Take a look at the realisation in the following short film 🎥⇣
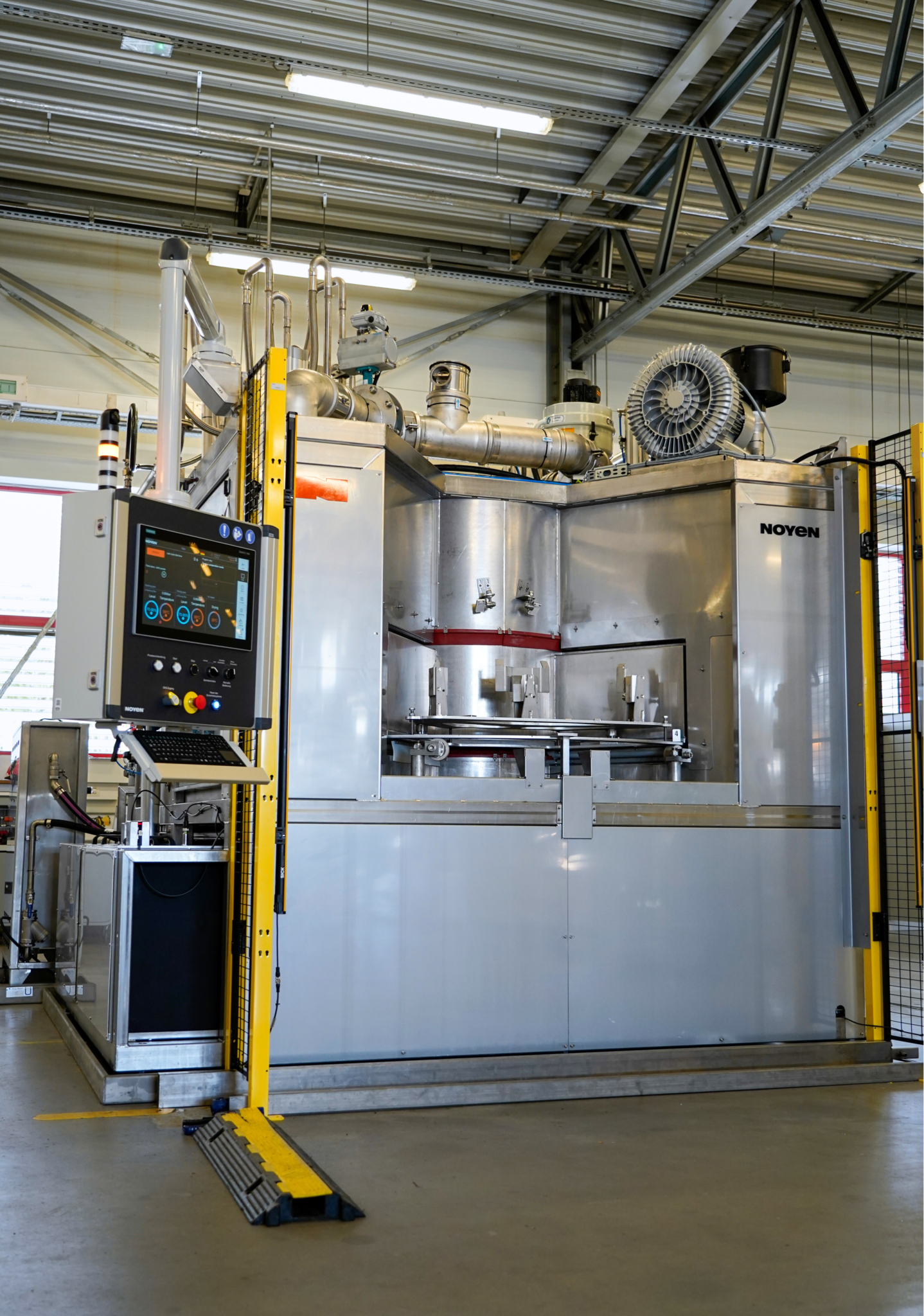
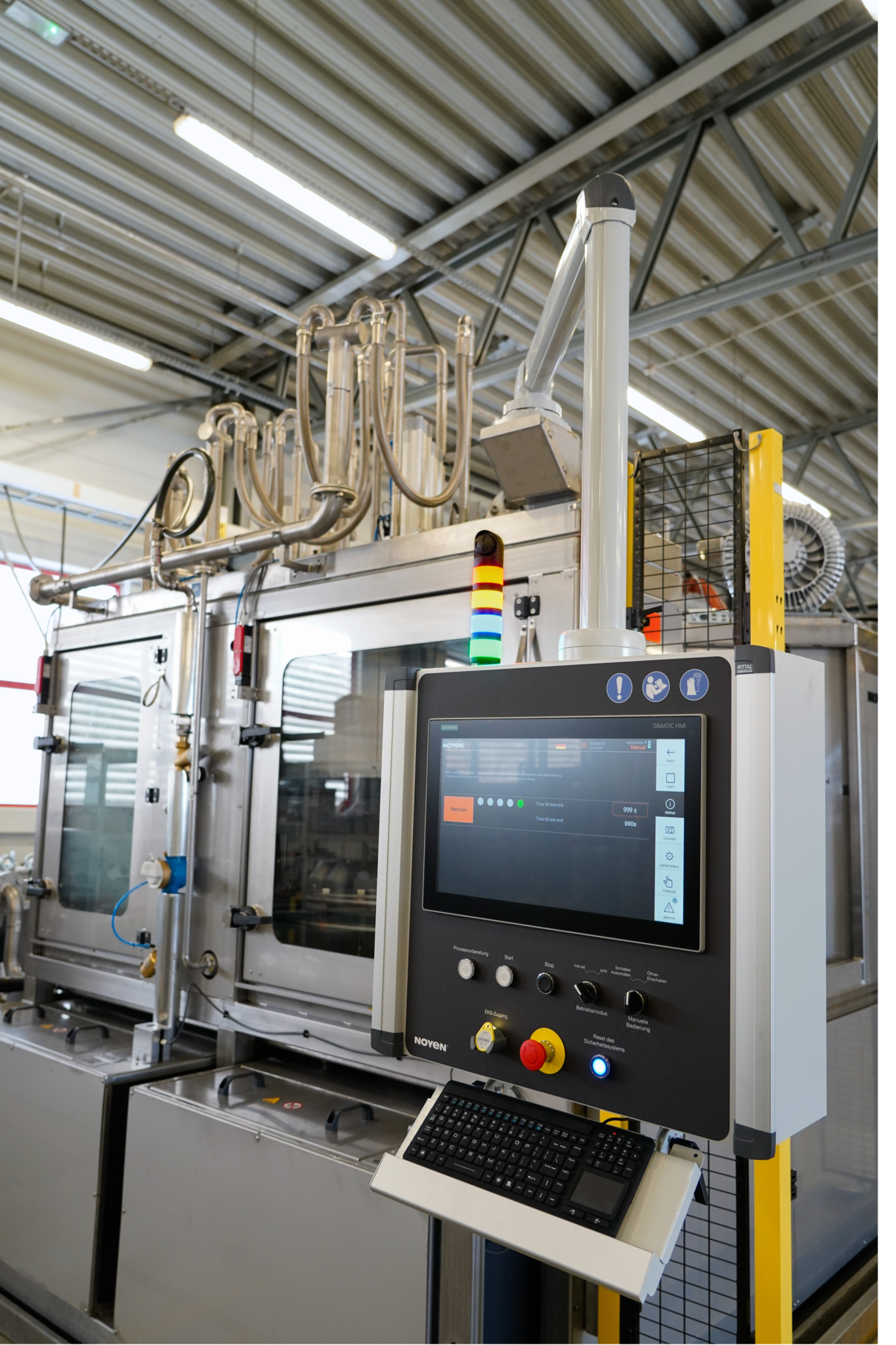
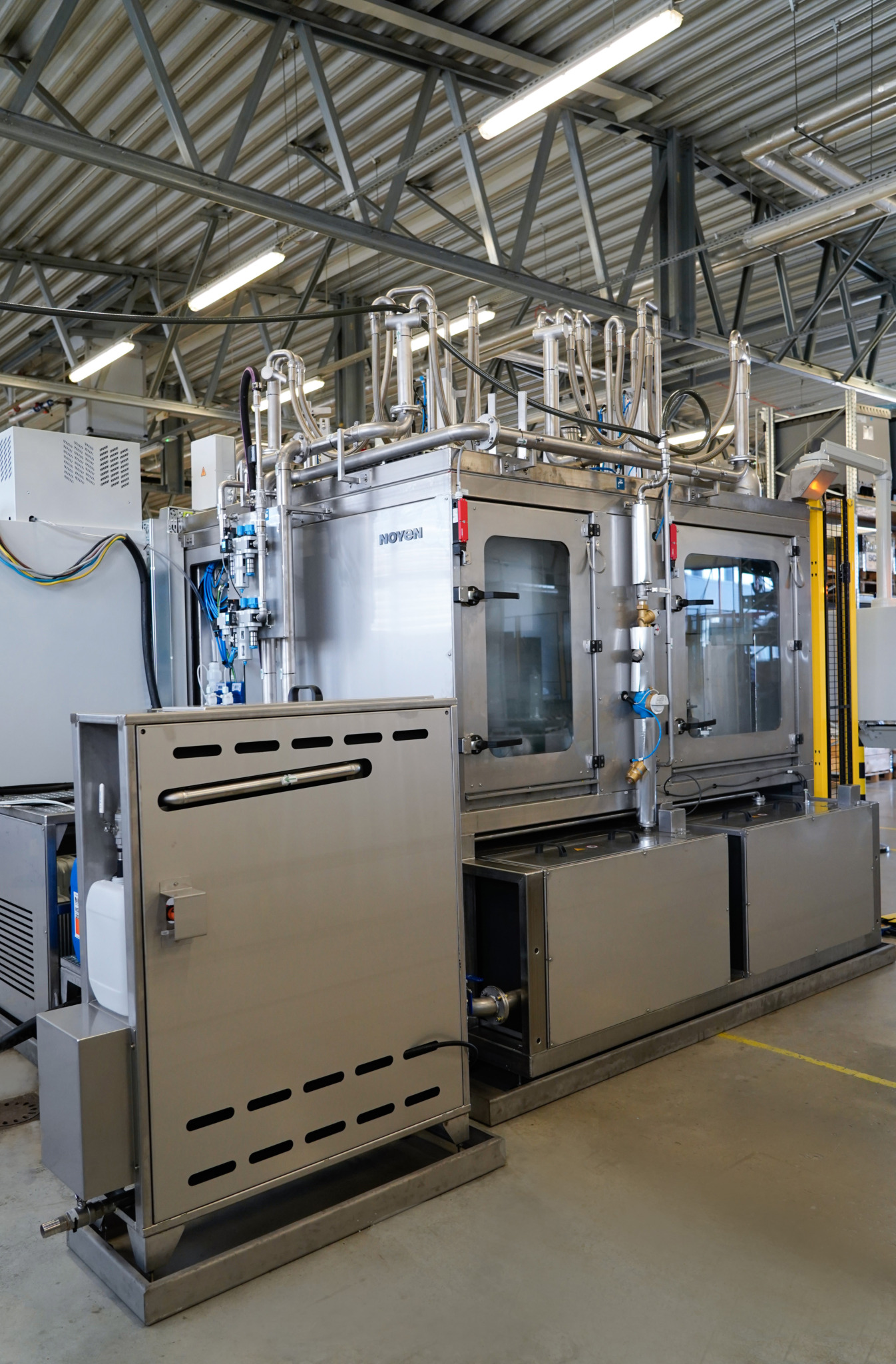
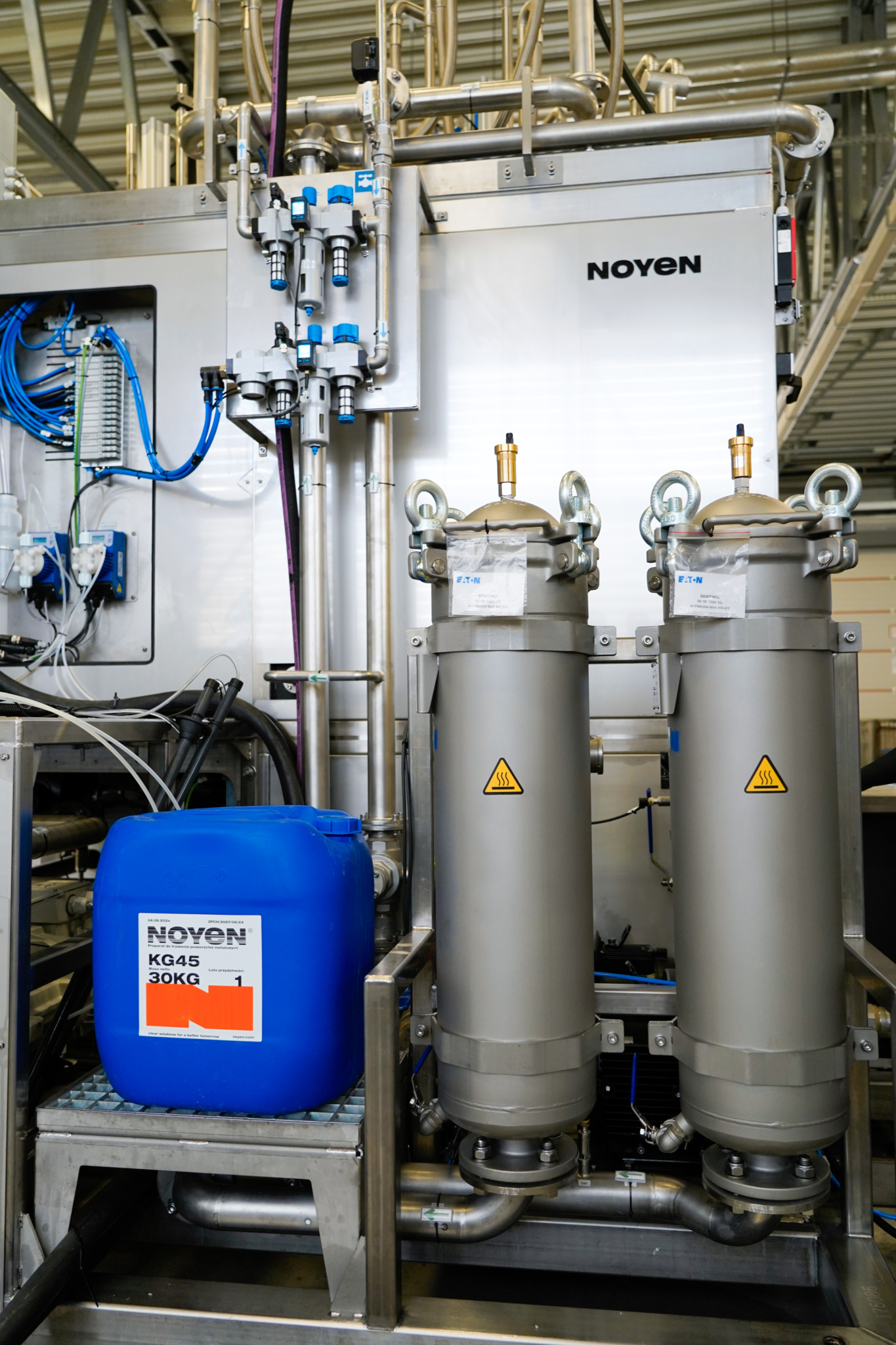
Nothing is impossible
It will be much easier if you tell us what is the matter. Save some time and sign up for a free consultation. Our expert will advise you free of charge.